在鈑金加工領域,實現板材的多角度錯動折彎能夠為產品賦予結構與外觀,滿足多樣化的設計需求。錯動折彎機憑借其特殊的功能,成為達成這一目標的有力工具。
加工前準備:精準規劃與模具適配
-
設計規劃:首先,借助 CAD/CAM 軟件進行詳細的設計規劃。依據產品的最終形狀與功能要求,精確繪制板材的折彎圖樣,明確各個折彎角度、錯動方向與距離。例如,對于一個具有復雜外觀的電子產品外殼,需精準規劃每個面的折彎角度以及相鄰面之間的錯動關系,確保各部分尺寸精準無誤,為后續加工提供精確指導。
-
模具適配:依據設計規劃,選擇或定制適配的模具。模具的形狀、尺寸和精度直接影響折彎效果。對于常規角度,可選用標準模具;而對于特殊角度或復雜形狀的折彎,則需定制專用模具。比如,在加工航空零部件時,為實現特定角度的錯動折彎,常需定制高精度模具,確保模具的表面光潔度和平整度,以防止板材在折彎過程中出現劃痕或變形不均。
設備參數設定:精確調控保障折彎精度
-
角度參數設定:在錯動折彎機的控制系統中,精確輸入每個折彎步驟的角度參數。現代錯動折彎機多配備高精度的角度控制系統,可精確到小數點后一位。例如,若要實現 30.5° 的折彎角度,需嚴格按照設計要求輸入,同時考慮板材的回彈特性,通過試驗或經驗公式預先對角度進行補償,確保最終折彎角度符合設計標準。
-
錯動參數設定:依據設計規劃,設定錯動的方向與距離參數。錯動方向可分為水平、垂直或特定角度方向,錯動距離則需精確到毫米甚至更小單位。例如,在制造汽車內飾件時,為營造立體效果,需精確設定錯動距離為 2 - 3 毫米,確保各個錯動部位的一致性,提升產品的整體美觀度與質量。

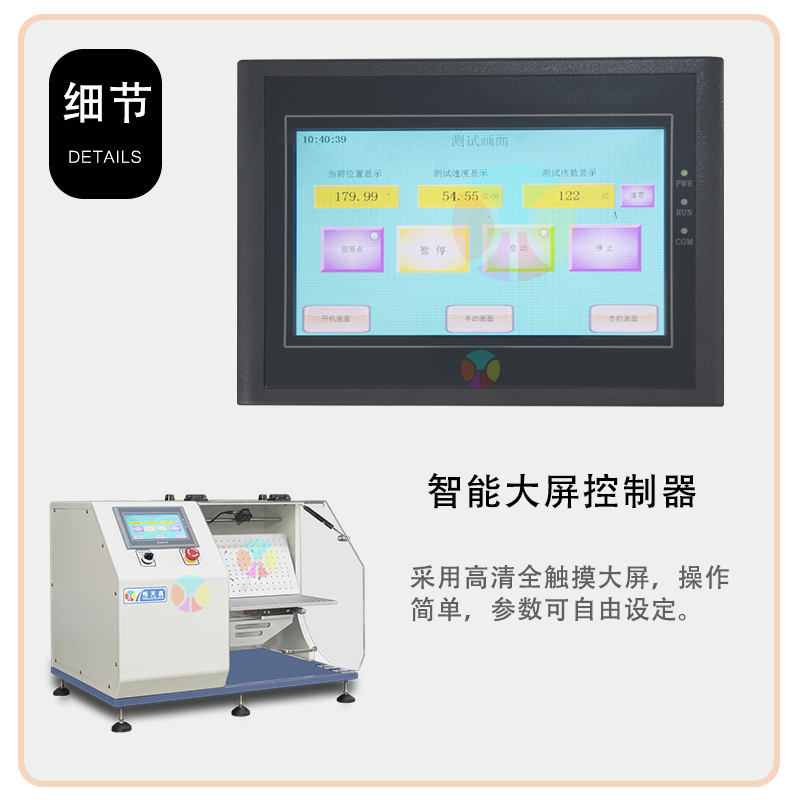
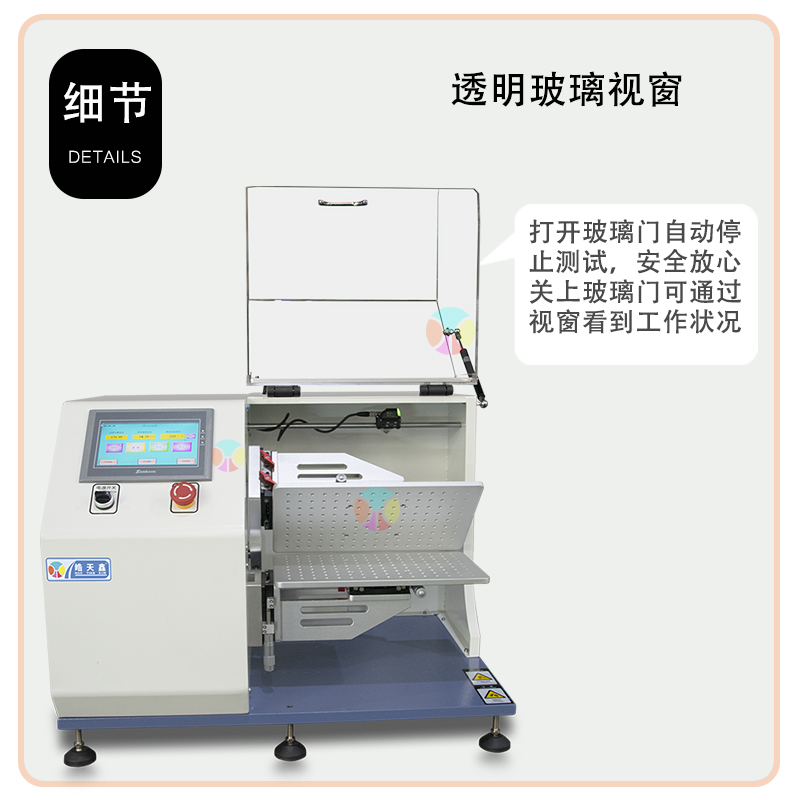
操作過程控制:規范流程確保加工質量
-
板材定位與裝夾:將板材準確放置在工作臺上,利用定位裝置確保板材位置精準。隨后,通過裝夾機構牢固夾緊板材,防止在折彎過程中發生位移。裝夾力度要適中,過大會導致板材變形,過小則無法保證定位精度。例如,在加工大型機械外殼板材時,可采用多點裝夾方式,確保板材在整個加工過程中保持穩定。
-
分步折彎與錯動操作:按照預先設定的參數,進行分步折彎與錯動操作。每完成一次折彎,根據設定的錯動參數,精準控制工作臺或模具的錯動,實現板材的多角度錯動折彎。在操作過程中,密切觀察設備運行狀態與板材的變形情況,如有異常及時調整。例如,在進行連續的多角度錯動折彎時,要確保每一步的折彎和錯動都準確無誤,保證板材的折彎過渡自然、流暢。
質量檢測與優化:嚴格把關提升產品品質
-
實時檢測:在加工過程中,利用角度測量儀、激光測距儀等檢測工具,實時監測折彎角度和錯動距離。對于批量生產的產品,進行全檢,確保各項參數符合設計要求后,再進行批量加工。例如,每隔一定數量的產品,對其折彎角度和錯動距離進行抽檢,及時發現并糾正可能出現的偏差。
-
優化調整:依據檢測結果,對加工參數進行優化調整。若發現折彎角度偏差,可適當調整折彎壓力、速度或角度補償值;若錯動距離不準確,則需檢查錯動機構的精度并進行相應調整。通過持續優化,不斷提升板材多角度錯動折彎的加工質量,滿足日益嚴格的產品質量要求。